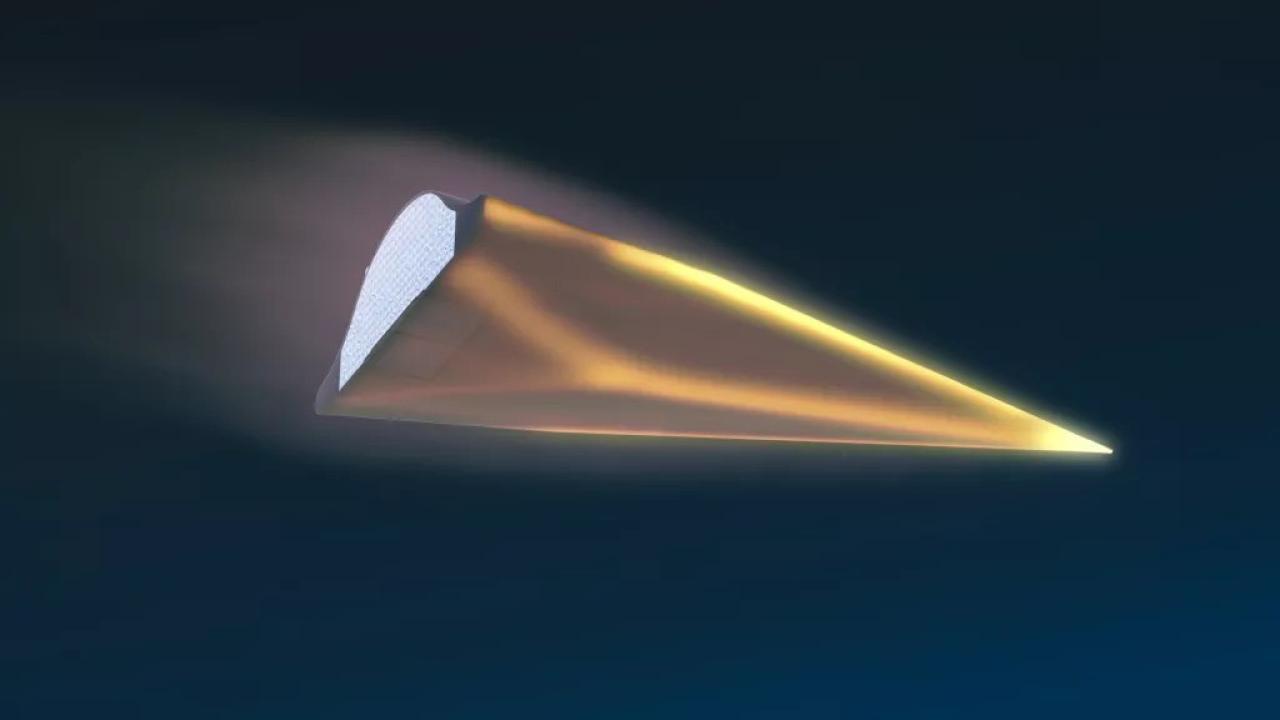
Scott McCormack Receives $1.4M to Study Ultra-High Temperature Ceramic Processing
Materials Science and Engineering Assistant Professor Scott McCormack and his team received $1.4M from the Air Force Office of Science and Research to reduce uncertainty and standardized processing techniques for ultra-high temperature ceramics.
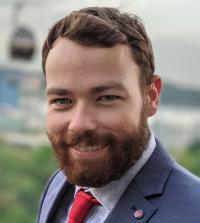
Ultra-high temperature ceramics (UHTCs) are ceramic materials that melt at temperatures above 3000˚C, nearly 5500˚F. Their ability to withstand extreme heat loads makes them ideal for building hypersonic vehicles and platforms, but UHTCs can be difficult to process reliably.
“Different labs will follow what they think is the same procedure, but the UHTC components have quite a high variability in their properties,” said McCormack. “It’s clear that something is happening that people haven’t been able to pin down exactly.”
McCormack and his collaborators at the University of Pittsburgh and Missouri University of Science and Technology plan to find out in the new three-year project. The team will study the promising UHTC zirconium diboride (ZrB₂) at each stage of manufacturing to study the relationship between processing, material microstructure and its resulting properties. They will then develop and validate a computational model that recommends the processing parameters required to produce UHTC components reliably.
“The core goal of the project is to reduce uncertainty when processing ultra-high temperature ceramics,” he said. “We’re developing a recipe with bounds that will allow us to say, ‘this is the impurity-range/processing time/pressure you need to reduce uncertainty.’”
Step-by-Step Analysis
UHTCs like ZrB₂ begin life as a powder made of tiny ball-shaped grains. They are then tightly pressed together like packed brown sugar in a process called densification. The densified material is baked in a furnace, where the balls turn little hexagons that form the material’s microstructure. In each step, the team will analyze the material’s flaws, also known as defects, and how they change.
“Ceramics’ properties are dictated by flaws, so flaw population is absolutely critical,” he explained. “Cracks form based on a flaw inside the material, so the more flaws you have, the higher the chance of a crack forming. You can increase the material’s toughness by essentially removing these flaws or reducing the critical flaw size.”
For the experiments, Bill Fahrenholtz at Missouri University of Science and Technology will process and characterize the ZrB₂ powders for the team to see if they contain random impurities. Then, in collaboration with Lawrence Berkeley National Lab’s Advanced Light Source, McCormack will track and 3D image the material’s microstructure during sintering.
“We’re going to do some in-situ sintering experiments to try and track defects that are forming as they’re forming,” he said. “We’ll be able to have the 3D microstructure just before and just after densification to see how defects are evolving during processing.”
They will then run material property experiments to see how the material changes once it’s baked into the final product.
Recommending Recipes
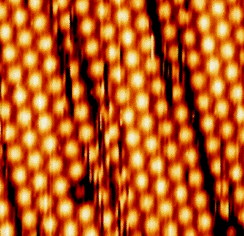
McCormack and Fahrenholtz will give their data to Wei Xiong and Hessam Babaee at the University of Pittsburgh, who will create a database of the processing-structure-property relationship and conduct statistical analysis and uncertainty quantification. The team will use this to train a model that can recommend ideal bounds and processing parameters for UHTC’s, given desired properties.
The final step is verifying that the model’s recommendations work with real-world examples. If successful, the project is the first step toward standardizing UHTC processing and making these materials readily available for building hypersonic platforms reliably.
McCormack looks forward to working with the Air Force Research Lab in Ohio and sending students to the lab each summer. He feels the students will gain valuable experience, training and connections they could use to launch their careers, while the group can establish a relationship with the lab.
He is excited to begin, not only because of the experiments and the collaboration, but also the opportunity for his group to branch out from fundamental research into more applied work.
“I’m very excited to use this project as a starting point for our lab’s research to go to a higher technology readiness level (TRL),” he said.