UC Davis Students Investigate Discoloration of High-Calcia Alumina
This article was published in the December 2021 issue of the ACerS’ Ceramic & Glass Manufacturing magazine.
As a high-tech manufacturing company that produces precision components for critical applications in several industries, Elcon Precision in San Jose, California is always investing in new technologies and developing better processes to not only meet customer specifications but also satisfy scientific curiosity.
One puzzle that Elcon has encountered for many years is discoloration of some alumina compositions during ceramic metallization, a service that Elcon offers. In this process, a proprietary thick film moly-manganese paint is applied to bare ceramic substrates to prepare them for subsequent brazing into assemblies. After metallization, parts undergo wet hydrogen firing at around 1,400°C. For aluminas with high calcia concentrations (1–2%), greyish discoloration is often observed on the surface of the ceramic. This phenomenon is often called nucleation.
Although nucleation does not reduce bond strength or affect the part’s physical or electrical properties, it is a cosmetic issue many customers prefer to avoid. Yet, to our knowledge, there is no published research on why this discoloration only occurs in certain aluminas and how it can be prevented.
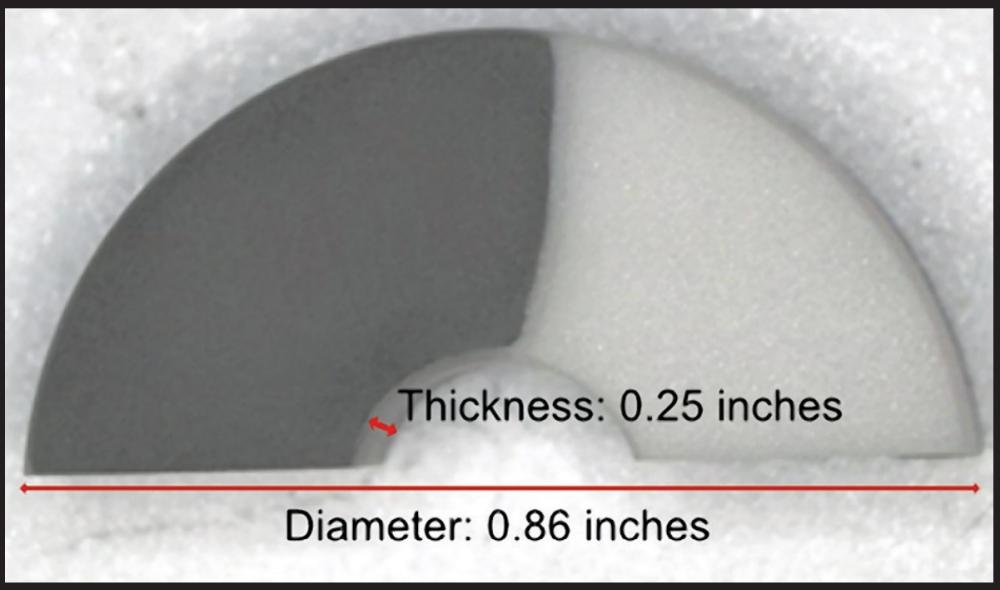
In the spring of 2021, Elcon had the opportunity to investigate this question when a team of undergraduate students at the University of California, Davis, reached out to Elcon to collaborate on a project. Rebecca Salcedo, Elcon’s process engineer, and Tim Dyer, Elcon’s president, agreed to support a project with six students from professor Subhash Risbud’s EMS 188 course: Rachel Altovar, Clayton Braga, Miranda Bell, Nicole Shuman, Ethan Suwandi, and Jiaying Li.
The students were excited to explore the question of nucleation and discoloration in high calcia alumina. As Shuman explains, “although our courses discussed topics such as viscosity and brittleness, there weren’t any courses where we focused on ceramics or polymers. The attraction for all of us with this project was the opportunity to broaden our knowledge and skills working with ceramics.”
The team took to the project enthusiastically and, with a 10-week project timeline, assigned roles best suited to their strengths—project manager, literature research, material characterization, computer modeling, and experimental design. The team focused on 97% and 97.5% aluminas from two different manufacturers that had 1–2% calcia concentration. Commonly used in defense and electronics applications, these aluminas contain calcia because the calcia acts as an alumina flux and reduces the sintering temperature significantly by formation of a calcia-alumina eutectic, which in turn reduces firing cycle times.
At Elcon, it often takes one to two weeks to get a sample run for a research and development project because resources are reserved for production. However, that approach would not have worked if the project was to meet its deadline, so the Davis team decided to start with computational modeling.
“Modeling allows you to test things before they actually happen,” Suwandi says. In the case of ceramic microstructures, which are very complicated systems, understanding the composition of the material and its reactive properties under simulated conditions can pave the way to running much faster and smoother experiments.
To develop an accurate model, the team reviewed academic papers by Klaus et al.,1 investigating the phase formation and thermal stability of the CaO–Al₂O₃–MgO system under different sintering temperatures and times. These papers showed that the ternary hexa-aluminate phases CAM I (C₂M ₂A1₁₄) and CAM II (CM₂A₈) can form at a narrow temperature range of 1,400–1,700°C. In addition, Martinez et al. found that hibonite can form as well in calcia-containing alumina materials processed between 1,150–1,500°C. These phases function as an interlock in the alumina matrix and strengthen the bonds of compounds, enhancing the substrate’s thermal and mechanical properties. This microstructure observation of an aluminate ceramic system under different sintering temperatures and times pointed the team to consider these factors as the cause of discoloration.
The team used Thermo-Calc, a modeling and prediction tool commonly used in industry, in conjunction with CALPHAD (CALculation of PHAse Diagrams) to produce high-resolution phase diagrams. CALPHAD uses a database of experimental and theoretical values including phase compositions at equilibrium to calculate the Gibbs free energy for a specific phase. Though Thermo-Calc hosts a robust methodology and database, there is little to no experimental data available for the ternary ceramic systems being analyzed. Using Thermo-Calc Python, the team rewrote the script to add flexibility to defining the phase boundaries and necessary kinetics. Having multiple sophisticated resources and systems provided by the university allowed the team to quickly adapt to the project’s needs.
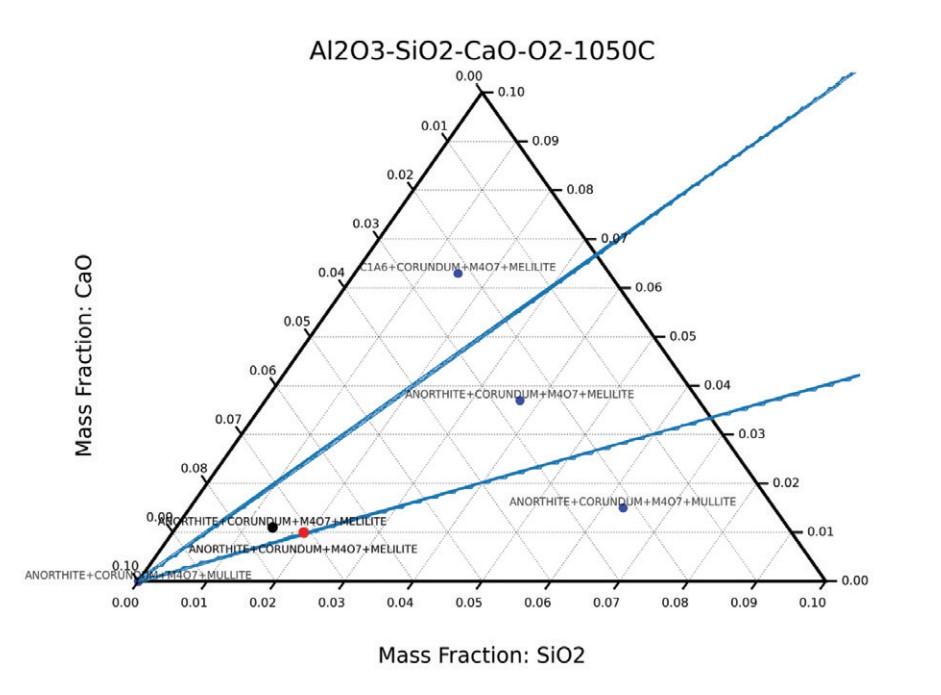
Armed with this set of tools, the modeling team input compositions for the high calcia alumina samples (Al₂O₃, SiO₂, and CaO) into the program using the metal oxide ceramics database. Modeling was performed in both atmospheric (1 atm) and vacuum conditions (1 x 10–7 atm) with a temperature range of 200°C to 1,750°C to create ternary phase diagrams. Alumina samples included both discs and thin boards of 97.5% alumina (Sample A) and 97% alumina (Sample B).
Several relevant phases were identified in the high calcia alumina models, including
- Corundum (Al₂O₃): Dominant phase. Colorless.
- Anorthite (CaO • Al₂O₃ • 2SiO₂): Forms in most phase regions. White to grayish.
- Hibonite (CaO • 6 Al₂O₃): Forms in both samples above ~1,000°C. Brownish/black
- Mullite (Al₆Si₂O₁₃): Forms in phase regions adjacent to 97% alumina at all temperatures. Colorless, but other technical ceramic papers show a graying effect around 1,400°C.
A significant finding from these phase diagrams was that hibonite developed in the firing temperature range where the surface discoloration occurs. Hibonite is an alumina-calcia phase that is known for forming brown and grey colors between 1,150–1,500°C. Furthermore, due to composition variations, the calcia-containing alumina samples have the disposition to form both mullite and hibonite. These findings led the team to form an early hypothesis that the discoloration was due to hibonite and/or mullite formation at temperatures above 1,000°C.
The team used these phase diagrams, the literature review, and historical production data provided by Elcon to design their experiments around this hypothesis. Designing the investigation around the phase diagrams and material compositions allowed the team to have a more directed approach while also applying their theoretical knowledge to a relevant experiment
Suwandi says that “Within the simulation and microstructure characterization research that I do, there’s a propensity for computational people to get stuck in their own world. Although you’re dealing with complex models, at the end of the day, if they’re not implemented into an experimental setting or connected to one, it kind of exists on its own. This project allowed us to apply these models to industry and pushed me onto a more specialized path, which consists of microstructure characterization and reconstruction.”
Conducted at Elcon Precision and Prairie Ceramics in San Leandro, the experiment consisted of making adjustments in the thermal profiles, i.e., various holds under high temperatures, quenching the ceramics with rapid and slow cooling rates, and subjecting the substrates to different heat treatments. In addition, thin 99.9% pure alumina boards were painted using mixed silica and calcia glazes to serve as proxy samples to study the phase composition of the ceramic surfaces over a wide range of chemistries. Lastly, there were a few trials in which the alumina disks were coated with a pure calcia wash, manipulating the surface composition.
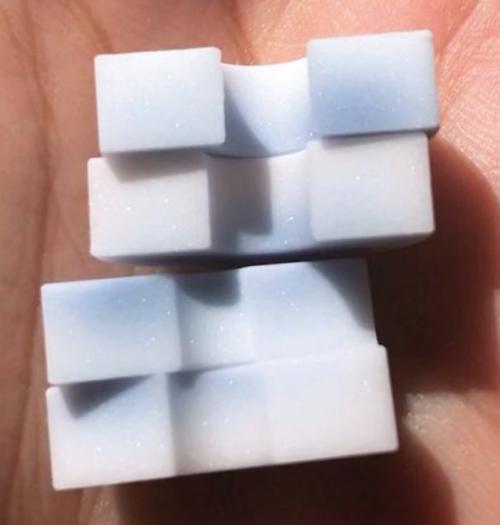
It is important to not only understand the phases present in the ceramics, but to also understand the phase dependence and the properties of each phase. This understanding can be accomplished with tools such as X-ray diffraction (XRD) and scanning electron microscopy (SEM). Using these methods can shed light on the origins and properties of the discoloration such as phase, thermostability, and temperature dependence. To understand the different phases present before and after metallization sintering, the alumina samples were characterized through XRD and SEM carried out in the Advanced Materials Characterization and Testing Laboratory at UC Davis. The unmetallized ceramic contains four major ternary compounds: gehlenite (Ca₂Al₂SiO₇), anorthite (CaAl₂Si₂O₈), clinopyroxene (CaAl₂SiO₆), and grossular (Ca₃Al₂Si₃O₁₂).
The diffraction patterns of the alumina samples generated by XRD were compared with the expected phase’s diffraction patterns to determine the phases existing in the samples. Diffraction patterns produced for sample A (97.5%) at 1,700°C and sample B (97%) fired at 1,450°C matched almost perfectly with that of corundum, suggesting that corundum is the major phase present (Figs. 4 and 5). Because it is a very common phase, identifying it prompts the hypothesis that a small amount of another phase is influencing the nucleation-based discoloration.
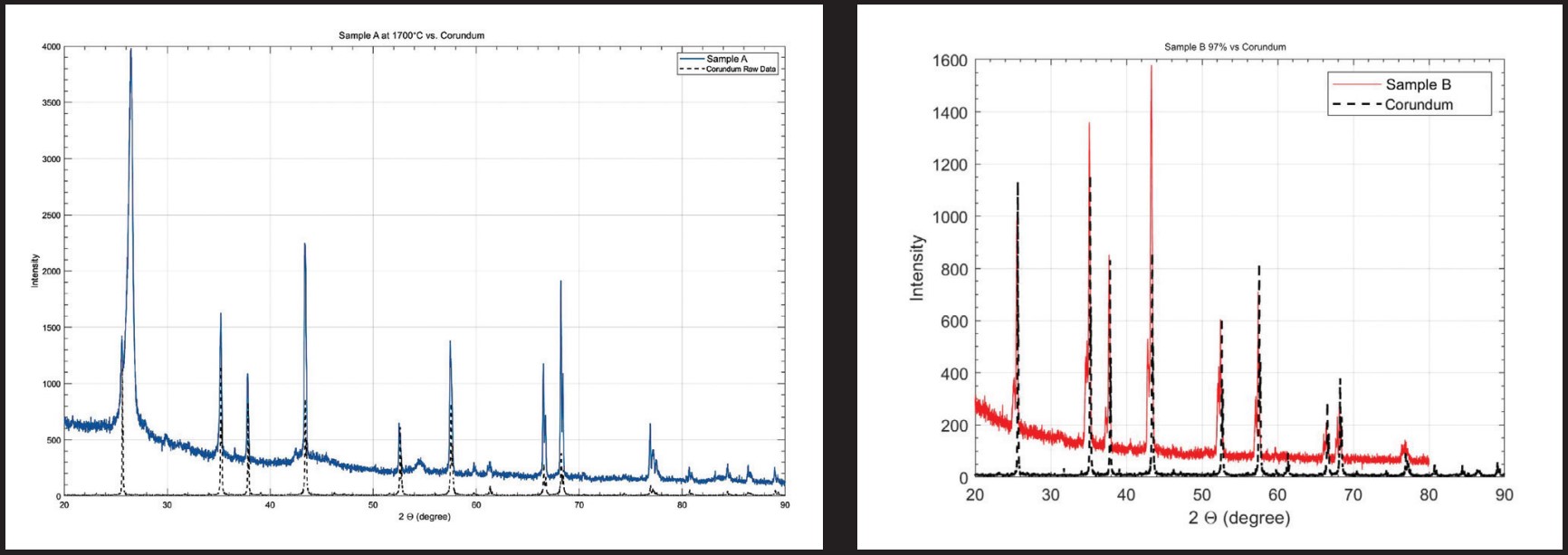
To improve XRD characterization of potential phase formation above 1,200°C, 99% alumina substrates were painted with a calcia-silica wash and then analyzed after metallization sintering. The diffraction patterns of some samples lined up closely with that of hibonite. This finding lends some support to the hypothesis that hibonite formed at specific temperatures, causing the discoloration.
SEM analysis of each alumina sample identified possible phases present on the surface. Based on these results, potential minority phases were identified—anorthite, mullite, and hibonite. These findings correlated with the phase diagrams generated from Thermo-Calc and also supports the hibonite formation hypothesis.
The team discovered that the discoloration created by metallization firing could be cleared by air sintering above 1,700°C followed by rapid cooling. A possible explanation for this solution is that hibonite is kinetically outcompeted by anorthite and corundum grain growth, possibly altering the local composition faster than hibonite can form.
Though the team accomplished the goal of exploring and disentangling the nucleation-based discoloration phenomenon, this academic–industry partnership sparked an even more significant realization. The culmination of literature reviews, computational modeling and characterization, and practical experiments not only accelerated learning, but it is a powerful problem-solving strategy that many companies still overlook. This team showed that using skills and expertise from both universities and companies collaboratively can improve materials processing performance.
When the students were asked what they wished to see more of regarding academic-industry partnerships in the future, Braga says he would “like to see more companies branch out and use university hires.” Supporting that, Suwandi believes that “there are a lot of opportunities for small companies, especially in the materials industry,” that should leverage the fact that “our curriculum is very theoretical, so we lack industry experience.” Suwandi adds that this project gave them an “experience with an entirely different set of rules and expectations than what goes on in the research side in a lab.”